Part Name | aluminum die casting/aluminum alloy die casting/copper alloy die casting/zinc alloy die casting .... |
Material Type | Aluminum alloy, Zinc alloy, Copper alloy, Magnesium alloy, Copper aluminum alloy; ADDC10, ADC12, A360, A380, ZL110, ZL101, ZDC1, ZD2, ZAMAK 3, ZAMAK 5, ZA8, ZL4-1, 6061-T5/T6, 6063-T5/T6 etc...(According to customer drawings and specifications) |
Machine Type | Die casting machine 120T, 180T, 280T, 400T, 630T, 800T. |
Additional machine | Punching machine <50T ~ ≥50T ~ ≥100T CNC machine, Electric Pluse, Wire EDM, Milling, Drilling, Grinding etc. Tapping Machine, Squeeze River, Spin Riveting machine Bending/Shearing machines. CNC machine, Electrinc pluse, Wire EDM, Milling, Drilling, Grinding etc. |
Surface Treatment | Polishing, Sandblasting, Painting, Powder coating ,Galvanizing, Chrome plating, Anodize (White or Black Color)  E-coating, T-Coating, as customer;s requirement. |
Process | Drawing & Samples → Mould making → Die casting → Deburring→ (Secondary processing if necessary) → Polishing → Surface treatment Quality inspection → Packing → Shipping |
Tolerance | +/-0.05mm or less. |
Application | -Lighting products -Electrical proudcts -Medical devices and products -Commercial and Industrial Equipment -Meters/recreational vehicles -Small engines, Vehicle parts |
Lead Time | Depends on the quantity and complexity of product. |
Drawing Type | .IGS . STEP . SLD . X_T . DXF .DWG . SAT . STL |
Company Information:
ShenZhen ShangHong Metals is a global manufacturer of both conventional and multi-slide die cast precision components. We offer solutions for a variety of industries including light of hoticulture and ballast, professional/stage lighting housings, LED light enclosures, motors, communication products, consumer electronics, automotive, healthcare, and more.Â
 All of our customers receive insight and expertise throughout all stages of the project. Contact us to request a quote today.
For more information, please visit our website: http://www.shanghongmetals.com
Our Factory:
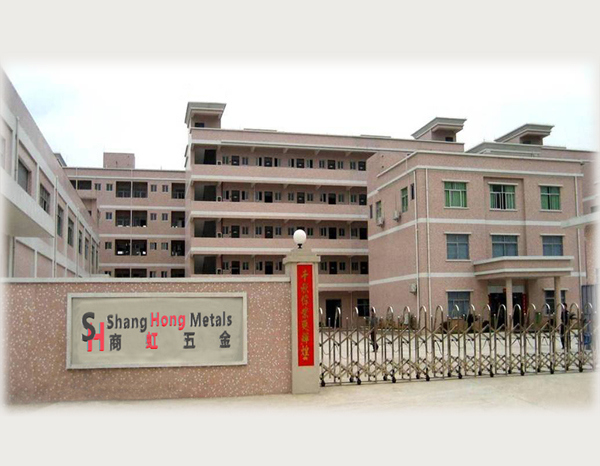
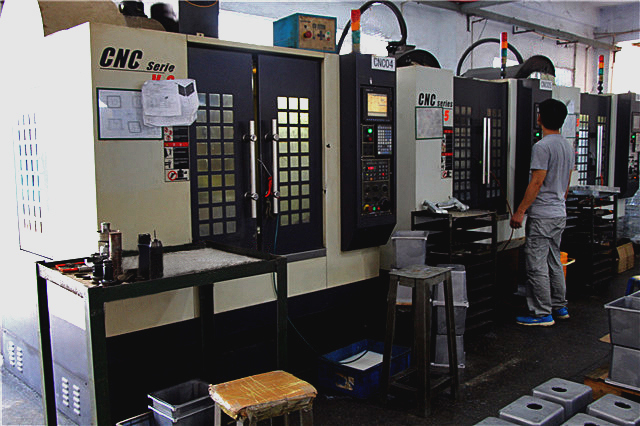
 Â
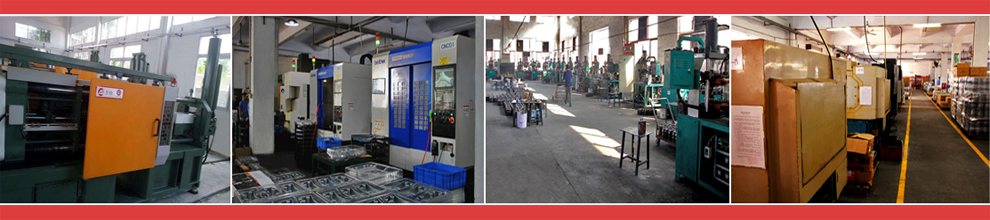
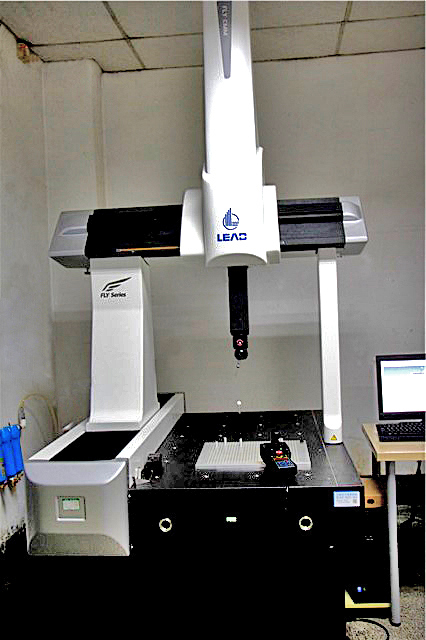
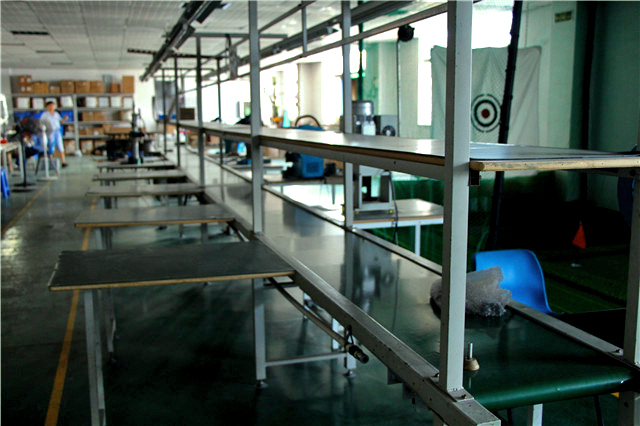
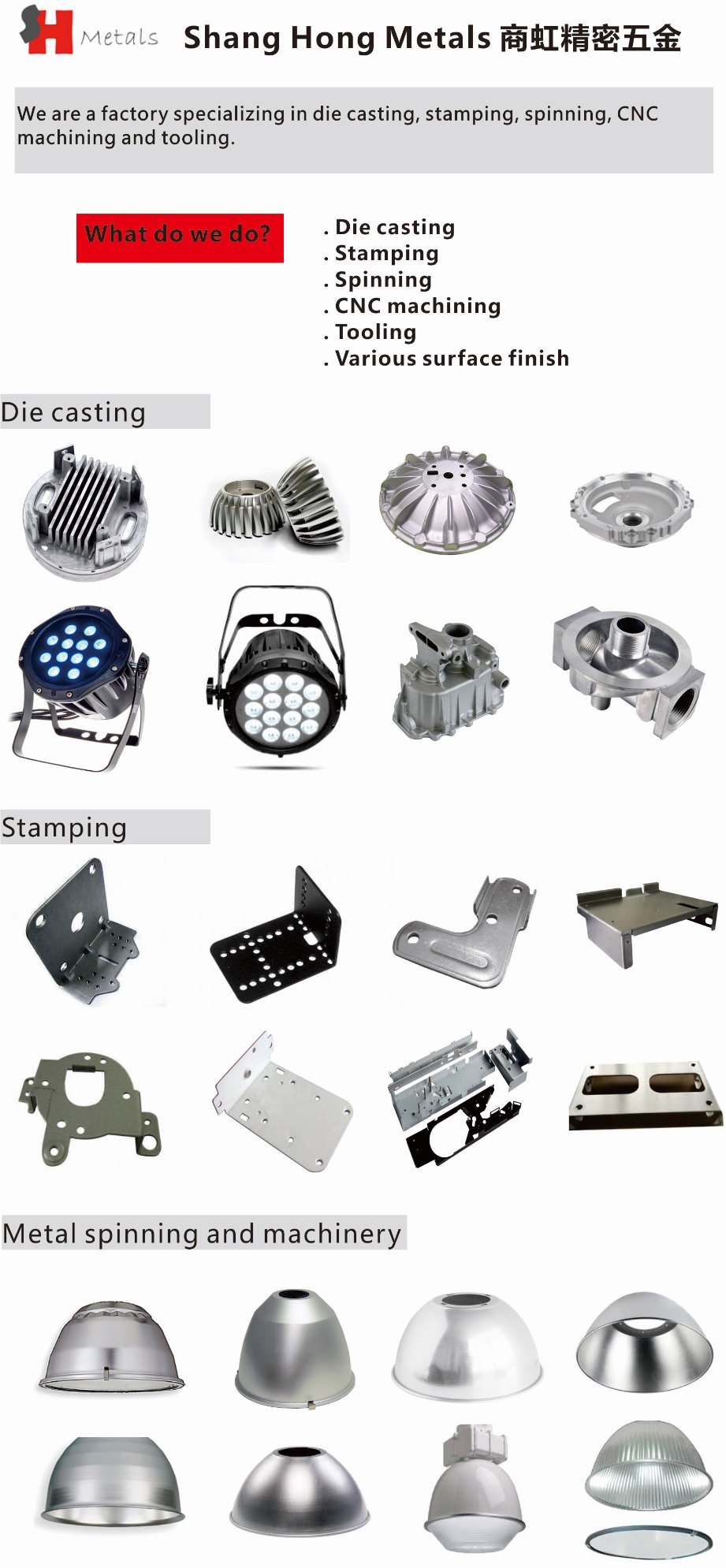
Die casting takes expertise that few possess. Different metals, processes, tooling, and machining all have to be taken into consideration before a part is produced. Our engineering and industry knowledge is what makes us, year-after-year, a leader in the die casting business.
Â
Die casting is a manufacturing process in which molten metal is poured or forced into steel molds. The molds-also known as tools or dies-are created using steel and are specially designed for each project. This allows each component to be created with accuracy and repeatability. Aluminum, zinc, and magnesium are the most commonly used die casting alloys.Â
Â
Die Casting Advantages
Die casting can have significant advantages over other manufacturing processes, which often lead to major cost savings, not only in the part price itself but also in the overall cost of production. When you cast a part, you can create complex net shapes, including external threads and complex internal features with minimal draft angles-minimizing secondary operations. You can also combine multiple parts into a single part, eliminating assembly operations and lowering labor costs, with the added benefits of simplified stock control and greater component consistency.
Other benefits include:
- Variable wall thicknesses
- Tighter tolerances
- Fewer steps from raw material to finished part
- Fast production cycle times
- Reduction in material scrap
- Long tool life, especially for zinc and magnesium
REGULATORS
You must be able to reduce the high-pressure gas in a cylinder to a working pressure before you can use it. This pressure reduction is done by a Regulator or reducing valve. The one basic job of all regulators is to take the high-pressure gas from the cylinder and reduce it to a level that can be safely used. Not only do they control the pressure but they also control the flow (volume of gas per hour).
Regulators come in all sizes and types. Some are designed for high-pressure oxygen cylinders (2,200 psig), while others are designed for low-pressure gases, such as natural gas (5 psig). Some gases like nitrous oxide or carbon dioxide freeze when their pressure is reduced so they require electrically heated regulators.
Most regulators have two gauges: one indicates the cylinder pressure when the valve is opened and the other indicates the pressure of the gas coming out of the regulator. You must open the regulator before you get a reading on the second gauge. This is the delivery pres-sure of the gas, and you must set the pressure that you need for your particular job.
The pressures that you read on regulator gauges is called gauge pressure. If you are using pounds per square inch, it should be written as psig (this acronym means pounds per square inch gauge). When the gauge on a cylinder reads zero, this does not mean that the cylinder is empty. In actuality, the cylinder is still full of gas, but the pressure is equal to the surrounding atmospheric pressure. Remember: no gas cylinder is empty unless it has been pumped out by a vacuum pump.
There are two types of regulators that control the flow of gas from a cylinder. These are either single-stage or double-stage regulators.
Single-Stage Regulators
Regulators are used on both high- and low-pressure systems. Figure 4-8 shows two SINGLE-STAGE regu-lators: one for acetylene and one for oxygen. The regulator mechanism consists of a nozzle through which the gases pass, a valve seat to close off the nozzle, a diaphragm, and balancing springs. These mechanisms are all enclosed in a suitable housing. Fuel-gas regulators and oxygen regulators are basically the same design. The difference being those designed for fuel gases are not made to withstand the high pressures that oxygen regulators are subjected to.
Figure 4-8.-Single-stage regulators.
In the oxygen regulator, the oxygen enters through the high-pressure inlet connection and passes through a glass wool falter that removes dust and dirt. Turning the adjusting screw IN (clockwise) allows the oxygen to pass from the high-pressure chamber to the low-pressure chamber of the regulator, through the regulator outlet, and through the hose to the torch. Turning the adjusting screw further clockwise increases the working pressure; turning it counterclockwise decreases the working pressure.
The high-Pressure Gauge on an oxygen regulator is graduated from 0 to 3,000 psig and from 0 to 220 in cubic feet. This allows readings of the gauge to deter-mine cylinder pressure and cubic content. Gauges are calibrated to read correctly at 70°F. The working pres-sure gauge may be graduated in [psig" from 0 to 150, 0 to 200, or from 0 to 400, depending upon the type of regulator used. For example, on regulators designed for heavy cutting, the working pressure gauge is graduated from 0 to 400.
The major disadvantage of single-stage regulators is that the working gas pressure you set will decrease as the cylinder pressure decreases; therefore, you must constantly monitor and reset the regulator if you require a fixed pressure and flow rate. Keeping the gas pressure and flow rate constant is too much to expect from a regulator that has to reduce the pressure of a full cylinder from 2,200 psig to 5 psig. This is where double-stage regulators solve the problem.
Double-Stage Regulators
The double-stage regulator is similar in principle to the one-stage regulator. The main difference being that the total pressure drop takes place in two stages instead of one. In the high-pressure stage, the cylinder pressure is reduced to an intermediate pressure that was predetermined by the manufacturer. In the low-pressure stage, the pressure is again reduced from the intermediate pressure to the working pressure you have chosen. A typical double-stage regulator is shown in figure 4-9.
Figure 4-9.-Double-stage regulator.
Problems and Safety
Regulators are precise and complicated pieces of equipment. Carelessness can do more to ruin a regulator than any other gas-using equipment. One can easily damage a regulator by simply forgetting to wipe clean the cylinder, regulator, or hose connections. When you open a high-pressure cylinder, the gas can rush into the regulator at the speed of sound. If there is any dirt present in the connections, it will be blasted into the precision-fitted valve seats, causing them to leak This results in a condition that is known as creep. Creep occurs when you shut of the regulator but not the cylinder and gas pressure is still being delivered to the low-pressure side.
Regulators are built with a minimum of two relief devices that protect you and the equipment in the case of regulator creep or high-pressure gas being released into the regulator all at once. All regulator gauges have blowout backs that release the pressure from the back of the gauge before the gauge glass explodes. Nowadays, most manufacturers use shatterproof plastic instead of glass.
The regulator body is also protected by safety devices. Blowout disks or spring-loaded relief valves are the two most common types of devices used. When a blowout disk ruptures, it sounds like a cannon. Spring-loaded relief valves usually make howling or shrieking like noises. In either case, your first action, after you recover from your initial fright, should be to turn off the cylinder valve. Remove the regulator and tag it for repair or disposal.
When opening a gas cylinder, you should just [crack" the valve a little. This should be done before attaching the regulator and every time thereafter. By opening the cylinder before connecting the regulator, you blow out any dirt or other foreign material that might be in the cylinder nozzle. Also, there is the possibility of a regulator exploding if the cylinder valve is opened rapidly.
WARNING
Oil or other petroleum products must never be used around oxygen regulators because these products will either cause a regulator explosion or fire
Regulator
Voltage Regulator,High Pressure Regulator,Gas Regulator
Changzhou Edaweld Trading Company Limited , https://www.edaweld.com